Setting Techniques for Tapered Roller Bearings
Proper maintenance and handling procedures are critical. Always follow installation instructions and maintain proper lubrication.Never spin a bearing with compressed air. The rollers may be forcefully expelled.Overheated bearings can ignite explosive atmospheres. Special care must be taken to properly select, install, maintain, and lubricate bearings that are used in or near atmospheres that may contain explosive levels of combustible gases or accumulations of dust such as from grain, coal, or other combustible materials. Consult your equipment designer or supplier for installation and maintenance instructions.Tensile stresses can be very high in tightly fitted bearing components. Attempting to remove such components by cutting the cone (inner race) may result in a sudden shattering of the component causing fragments of metal to be forcefully expelled. Always use properly guarded presses or bearing pullers to remove bearings from shafts, and always use suitable personal protective equipment, including safety glasses.
If hammer and bar are used for installation or removal of a part, use a mild steel bar (e.g., 1010 or 1020 grade). Mild steel bars are less likely to cause release of high-speed fragments from the hammer, bar or the part being removed. Remove oil or rust inhibitor from parts before heating to avoid fire or fumes.
Do not use damaged bearings.Use of improper bearing fits may cause damage to equipment.
Please consult with your Timken engineer for more information and assistance.
NOTE
Do not use excessive force when mounting or dismounting the unit.Follow all tolerance, fit, and torque recommendations.Always follow the Original Equipment Manufacturer’s installation and maintenance guidelines.Ensure proper alignment.Do not heat components with an open flame.Do not heat bearing beyond 300° F.Unless directed otherwise by Timken, products should be kept in their original packaging until they are ready to be placed in service.Do not attempt to disassemble unitized bearings.Components may become damaged and affect the performance and service life of bearing.
DISCLAIMER
Every reasonable effort has been made to ensure the accuracy of the information in this writing, but no liability is accepted for errors, omissions or for any other reason.
SETTING TECHNIQUES FOR TAPERED ROLLER BEARINGS
TAPERED ROLLER BEARING SETTING TECHNIQUES
Tapered roller bearings can be set at initial machine assembly to any desired axial or radial clearance. This unique feature enables a designer to control bearings to meet anticipated application operating conditions, and thereby provide optimum bearing and system performance.
Some advantages of tapered roller bearings pertaining to setting include:
- Longer bearing life, achieved by optimizing bearing settings while meeting application performance requirements.
- Increased mounting stiffness, achieved by properly set tapered roller bearings resulting, for example, in better gear contact and longer gear life.
- Easier assembly because cone and cup are separable.
- The bearings can be set at the time of machine assembly, allowing wider shaft and housing tolerances.
The setting of tapered roller bearings can be readily accomplished by a wide variety of viable methods. These bearings can be set manually, supplied as preset assemblies, or set by automated techniques. There are a number of approaches, considerations and advantages of each with special focus on five popular automated techniques (i.e. SET- RIGHT TM , ACRO-SET TM , PROJECTA-SET TM , TORQUE-SET TM , and CLAMP-SET TM ). SeeTable 1.
BEARING SETTING
With tapered roller bearings, the term “setting” simply indicates the specific amount of end play (axial clearance) or preload (axial interference) within a mounted bearing. The flexibility to easily adjust and optimize setting at the time of assembly is an inherent advantage of tapered roller bearings. Unlike other types of anti-friction bearings, tapered roller bearings do not require tight control of shaft or housing fits to obtain setting. Because tapered roller bearings are mounted in pairs (Figure 1), their setting is primarily dependent upon the axial location of one bearing row relative to the opposite row.
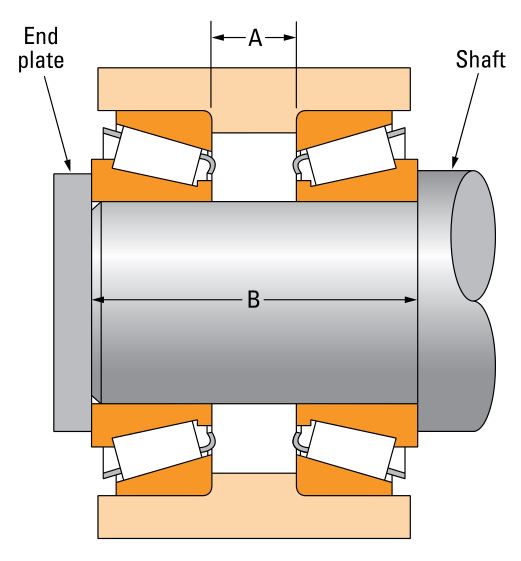
The three primary conditions of bearing setting are defined as:
- End play — An axial clearance between rollers and races producing a measurable axial shaft movement when a small axial force is applied, first in one direction and then in the other, while oscillating or rotating the shaft (the reference bearing load zone less than 180 degrees).
- Preload — An axial interference between rollers and races such that there is no discernible axial shaft movement when measured as described above. A rolling resistance to shaft rotation results which may be measured (load zone greater than 180 degrees).
- Line-to-line — A zero setting condition, the transitional point between end play and preload.
Bearing setting obtained during initial assembly and adjustment is the cold or ambient bearing setting and is established before the equipment is subjected to service. Bearing setting during operation is known as the operating bearing setting and is a result of changes in the ambient bearing setting due to thermal expansion and deflections encountered during service. The ambient bearing setting necessary to produce the optimum operating bearing setting varies with the application. Application experience, or testing, generally permits the determination of optimum settings.Frequently, however, the exact relationship of ambient to operating bearing settings is unknown and an educated estimate has to be made. To determine a suggested ambient bearing setting for a specific application, contact a Timken sales engineer or representative.
TABLE 1 – COMPARISON OF TAPERED ROLLER BEARING SETTING METHODS
Generally, the ideal operating bearing setting is near- zero to maximize bearing life. Most bearings are set with a cold setting of end play at assembly. This comes as close as possible to the desired near-zero setting when the unit reaches its stabilized operating temperature.
Some applications are set with cold preload to increase rigidity and axial positioning of highly stressed parts that would otherwise be dramatically affected by excessive deflection and misalignment.
Excessive operating preload must be avoided as bearing fatigue life can be drastically reduced. Also, excessive operating preload can lead to lubrication problems and premature bearing damage due to high heat generation.
Load zone is a physical measure of the raceway loaded arc and is a direct indication of how many rollers share the applied load. For a single-row tapered roller bearing, maximum life is obtained with a load zone of approximately 225 degrees. Figure 2 shows the graphical representation of bearing L10 life versus operating bearing setting for a typical (overhung) pinion bearing mounting.
The ideal operating setting that will maximize bearing system life is generally near-zero to slight preload.
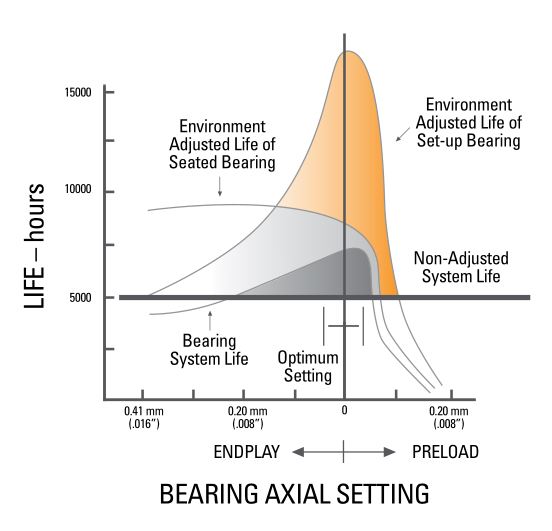
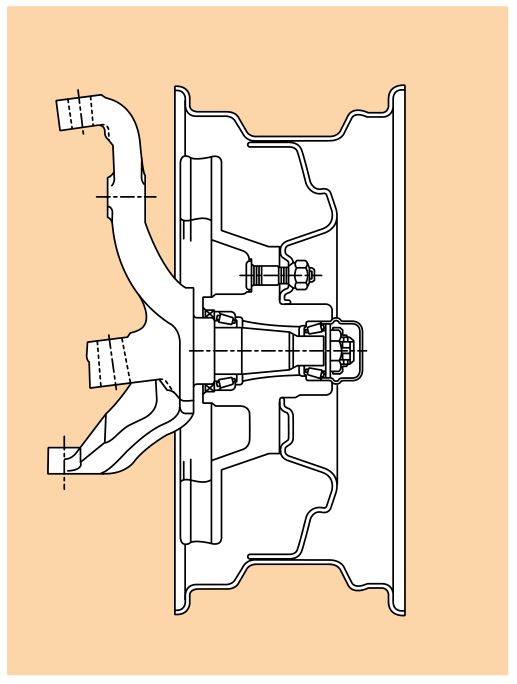
MANUAL BEARING SETTING
Manual methods are frequently used to set bearings on a variety of equipment with low to moderate volume production requirements whereby a non- exact, primarily end play, setting range variation is acceptable. No special tooling, gauges, charts or fixtures are typically required, but assembler’s skill and judgment are necessary. For example, in the case of a conventional truck non-driven wheel with a single adjusting nut design (Figure 3), manual setting involves tightening the adjusting nut while rotating the wheel until a slight bind is felt. Then the adjusting nut is backed off 1/6 to 1/4 turn to the nearest locking hole or sufficiently to allow the wheel to rotate freely with some minimal end play. The adjusting nut is then locked in this position. Skill and judgment are required to determine when the wheel binds slightly in rotation. The more complicated the equipment and/or the larger and heavier it is, the greater degree of skill and judgment required.
For certain complex designs, large equipment or high production applications, manual setting may be too troublesome, of inappropriate accuracy and reliability, or too time consuming. The Timken Company has devised preset bearing assemblies and automated setting techniques as alternatives to manual setting.
PRESET BEARING ASSEMBLIES
Many applications utilize or require the use of two- row or close- coupled bearing assemblies. This will depend upon the design and operating characteristics of the machine (e.g. thermal growth effects, high loads, etc.). To facilitate bearing setting of this type of design, preset bearing assemblies are frequently used. Preset bearing assemblies are available in a variety of forms, styles and arrangements, but for the most part are typically referred to as spacer bearings (Figure 4). The majority of preset bearings are manufactured and supplied with spacer rings “custom fitted” between the bearing rows to control the internal clearances (ref.“2S” and “TDI” types). As such, these customized or “matched” spacers cannot be interchanged with any other bearing assembly. Other preset assemblies such as “SR” or “TNA” types may apply interchangeable spacers and/or bearing components. Such interchangeable assembly components are designed to hold closer control of the critical tolerances that affect bearing setting, and as a result, they can be randomly selected.
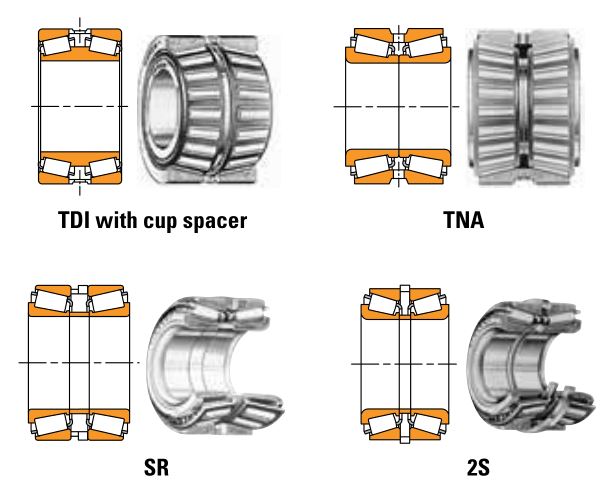
Each preset bearing is supplied from the manufacturer with a specified (unmounted) internal clearance or bench end play (BEP). This BEP is chosen to provide the desired mounted setting range for the given application requirements. The mounted bearing setting range is determined from this BEP based strictly on the effect of shaft and housing fits. Typically only one tight fitted (shaft or housing) requirement is applied (i.e. on rotating member). This results in expected mounted setting ranges of less than 0.008”. The mounted setting range of interchangeable component assemblies is typically wider than that for “matched” spacer assemblies. To apply preset assemblies in an application, simply mount and ensure proper clamping of the bearing components through the spacers.
TYPICAL PRESET BEARING ASSEMBLY APPLICATIONS
Preset bearing assemblies are widely and frequently used in many industrial applications. Typically this includes application in: planet pinions, hitch or linkage positions, transmission idler gears, fan hub shafts, water pump and idler pulley shafts, sheaves, conveyor idlers, winch drums, at the fixed and float positions of mining equipment, propel and swing drives, and in larger gear box drives.
AUTOMATED BEARING SETTING TECHNIQUES
In addition to preset bearing assemblies, The Timken Company has developed five popular automated bearing setting techniques (i.e. SET-RIGHT, ACRO- SET, PROJECTA-SET, TORQUE-SET, and CLAMP-SET) as alternatives to manual adjustment.
Reference Table 1 “Comparison of tapered roller bearing setting methods” provides a matrix format of various features of these techniques. Each method’s ability to hold a reasonably controlled mounted bearing setting “range” is compared on the first line of this table. These values are simply an indication of overall variability in setting for each method and have nothing to do with the “preload” or “end play” setting target. For example, under the SET-RIGHT column, the expected (probable or 6 sigma) setting variation, due to control of certain bearing and housing/shaft tolerances, could range from a typical minimum of 0.008” upwards to 0.014”. This range of setting can then be apportioned between end play and preload to best optimize the bearing/ application performance.
Reference Figure 5 – “Application of Automated Bearing Setting Techniques.” This figure utilizes a typical 4WD farm tractor design to demonstrate examples of the common application of tapered roller bearing setting methods. The specific definition, theory and formal process for the application of each technique will be discussed in detail, in the following sections of this module.
SET-RIGHT
SET-RIGHT eliminates manual setting adjustment of tapered roller bearings by controlling certain bearing and mounting system tolerances. The statistical laws of probability are applied to predict the affect of these tolerances on the bearing setting. Generally, the SET-RIGHT method requires closer control of some shaft/housing machining tolerances as well as closer control (with special class and code) of criticalbearing tolerances.
The method considers that each component involved in the final assembly of a machine has a controllable tolerance range for critical dimensions. The laws of probability indicate that combinations of all low tolerances or all high tolerances will rarely occur in such an assembly. It then follows that for a “normal tolerance distribution” (Figure 6), the overall dimensional stack-up of all parts will statistically tend to be somewhere in the middle of the total possible tolerance range.
The goal of the SET-RIGHT method is to control only the most critical tolerances affecting bearing setting. These tolerances may be completely contained within the bearing or may involve certain mounting components (i.e. widths A and B of Figure 1 or 7, plus shaft OD and housing ID). The result is an acceptable bearing setting that will occur within a desired range, with a defined statistical probability/reliability for all assemblies.(A probable reliability of 99.73% or 6 sigma is typical, but in higher volume production, a 99.994%, or 8 sigma reliability is sometimes required). There are no adjustment steps required to use the SET-RIGHT concept. The components of the machine are simply assembled and clamped.
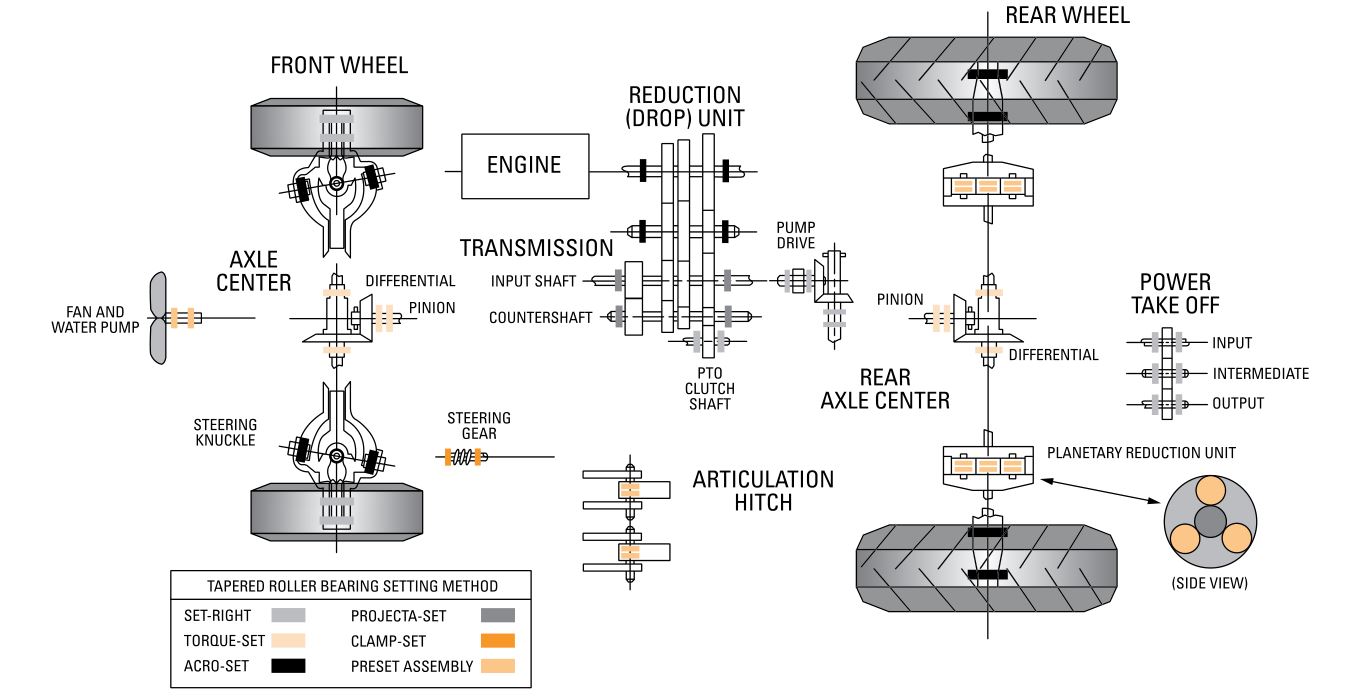
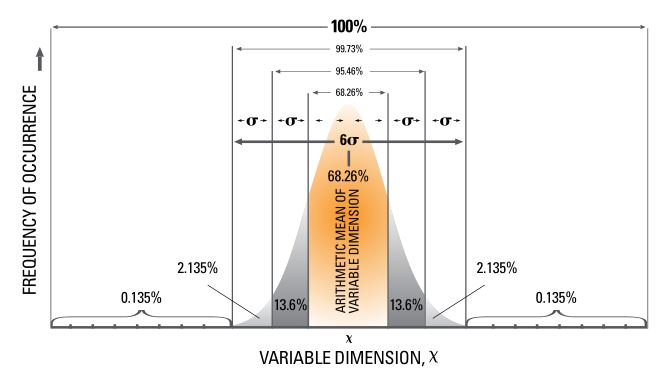
All dimensions affecting the bearing setting in a machine assembly, such as certain bearing tolerances, shaft OD, shaft length, housing lengths, and housing bores, are considered as independent variables when calculating the probable range. In this example, Figure 7, both cones and cups are mounted with conventional tight fits and the end plate is simply clamped against the end of the shaft.
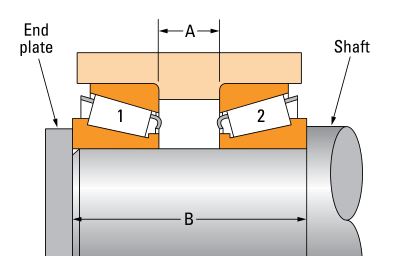
SPECIAL SET-RIGHT CONSIDERATIONS:
- The overall calculated bearing setting range can vary significantly depending on the bearing K- factor, its equivalent axial tolerance, and the number of tight fitted components applied (i.e. larger with both tight cones and cups). A review of the application during the design stage will enable a Timken sales engineer or representative to select special tolerance- controlled bearings and assist in optimizing the mounting design for the smallest probable setting range.
- Control of Bearing Mounting DimensionsThe tolerances of the bearing system mounting dimensions used in establishing the probable setting range must be consistently maintained and in some cases more tightly controlled.
- If the probable bearing setting range cannot be tolerated by the application, and attempts to reduce the larger tolerances are not practical or successful, then consider the SPIN-RIGHT variation to SET-RIGHT.
- The same class and code of bearing must be used for field service replacement as was used for the initial production.
SPIN-RIGHT VARIATION OF THE SET-RIGHT TECHNIQUE
In some cases, the probable bearing setting range with SET-RIGHT can be too large for the application. To reduce this range and still apply the laws of probability, a technique called SPIN-RIGHT is used. This technique can be applied to applications that could also lend themselves to “shim pack” adjustment (Figure 16). To apply the method, the existing probable range is simply divided by a factor of two or three depending on which is necessary to result in an acceptable setting range for the application.
For example, assume the probable bearing setting range for the design in Figure 1 is calculated to be 0.018” and the application demands a setting of 0.000” to 0.009” end play. The current range must be divided by a factor of two. Thus with SPIN- RIGHT, the desired shim increment (apply shim between endplate and shaft) would be equal to 0.009” and the following technique applied:
- Assemble the gearbox without a shim and “spin check”– without the seal in place – to determine if the bearings are set with end play or preload. Under the first spin check, if the shaft spins freely, end play is present (Figure 8) and the bearings are properly set.
- If the shaft does not spin freely, the bearings are preloaded. Then a 0.009” shim must be installed. A second “spin check” should result in a freely rotating assembly indicative of end play.
- If preload is the desired setting, the SPIN-RIGHT procedure would be applied in reverse of the above example: if the shaft rotates freely, the bearings are not properly set, and a shim of 0.009” would need to be removed.
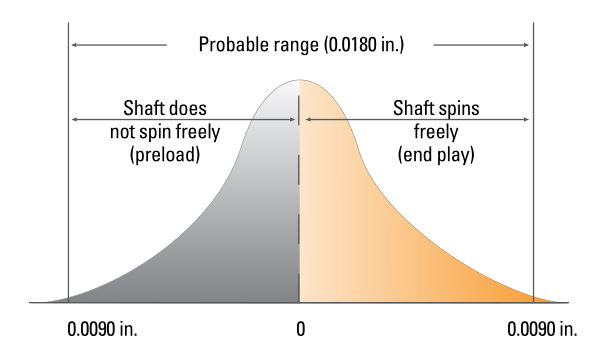
TYPICAL SET-RIGHT APPLICATIONS
The SET-RIGHT technique has been used for a wide variety of bearing setting applications which include: tractor PTO assemblies especially with blind end or split housing designs, automotive front drive wheels, gear reducer shafts, planet pinions, and sprockets and torque hub units as used on construction and mining equipment.
ACRO-SET
This widely used setting technique is based on Hooke’s law which states: within the elastic material limit, component deflections are proportional to the load applied (i.e. F = kx, where k = system spring rate). This method assumes that total system deflection of an assembly will be consistent and repeatable for a given applied load (Figure 9) in an application where parts and sections of parts are reasonably uniform throughout a group of units.
To establish the method for a given machine configuration, a dimensional reference condition known as the deflection constant must first be determined. The deflection constant is simply the (averaged) system deflection, resulting from a known “set-up” load applied through the bearings, as determined from the testing of several preproduction units. This system deflection is typically gauged by measuring a shim gap (Figure 10).
The ACRO-SET system constant is then developed. It equals the deflection constant for a given applied “set-up” load, plus the desired bearing setting. In production, this constant is added to the measured shim gap to determine the final shim pack thickness for each unit. Contact a Timken sales engineer or representative for assistance in setting the ACRO-SET system constant.
The selection of the final shim pack thickness for each unit can be simplified by the use of a shim chart (Figure 11). The shim pack thickness indicated on the chart includes the effect of the previously established ACRO-SET constant. Note that the shim chart facilitates proper shim pack determination based on shim gap measurements taken at two positions 180o apart. The planetary drive wheel assembly (Figure 10) will be used to illustrate the ACRO-SET technique.
- The “set-up” load “P” was established by pretesting and is applied by 2 capscrews (180 o apart). The applied load is proportional to the bolt torque. (Commonly, a much larger “seating” force is first applied and the bearings rotated to ensure proper assembled positioning of the components prior to the ACRO-SET shim gap measurement.)
Figure 9. System Deflection Figure 10. Planetary Drive Wheel - Rotate or oscillate the bearings while applying the “set-up” load “P” and measure the shim gap, first at 0 degrees and again at 180 degrees.
- Select the proper shim pack thickness (from the shim chart) equal to the measured gap plus the predetermined ACRO-SET system constant (that was established from pretested assemblies). The Figure 10 chart averages the two readings and provides the final shim pack thickness. In this case, 0.66 at 180 degrees and 0.61 at 0 degrees gives a 0.97 thick shim pack.
- Install the final shim pack and torque up all capscrews to their clamp-up torque.
FIGURE 11 – TYPICAL ACRO-SET SHIM CHART
SPECIAL ACRO-SET CONSIDERATIONS:
- Bearing “seating” and “set-up” loading is typically applied with multiple capscrews (i.e. Load = NT/(dμ) where: N = # of capscrews, T = capscrew torque, d = capscrew diameter, and μ = coefficient of thread friction; where typical μ = 0.17). Commonly, the applied seating force should be 2-3x Ca(90) and the applied set-up force chosen as 3/4 – 1x Ca(90) of the lowest capacity bearing in the system.
- Loose Fitted Adjustable ComponentA loose fitted member at the adjustable position is preferred. However, variations to tight fitted cups and cones can be made as described below:
- The use of tight cups in carriers that are loose fitted in the housing.
- The use of a loose fitted “master” cup or cone for the bearing setting operation (mean fit compensated for in ACRO-SET constant).
- Fixture designs with built-in compensation for the tight fitted member (PROJECTA-SET).
- All components essential to the ACRO-SET concept, such as housing walls and cover plates, must have a fairly uniform section size in successive production units.
- The design must lend itself to applying a set-up load to the movable bearing race for adjustment.
- The bearings must be rotated or oscillated while applying the set-up load.
- The design must also lend itself to gap measurement of the movable member.
- The thickness of the actual shim pack used should be verified.
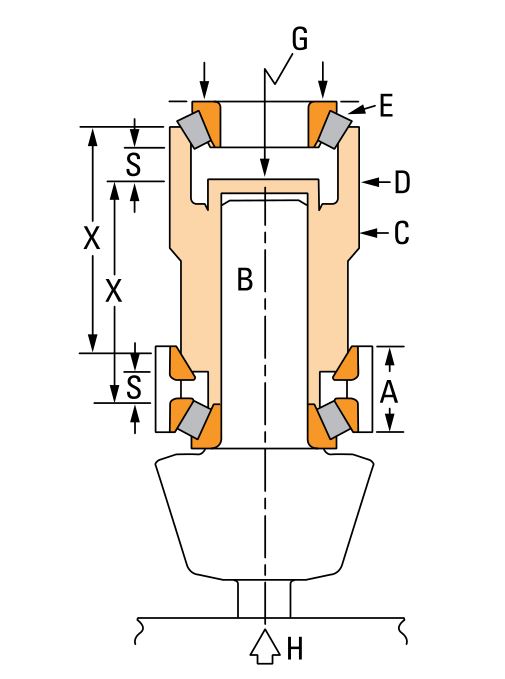
It may be seen from this simplified schematic that PROJECTA-SET is basically a method of ‘projecting’ the two faces essential to measuring the spacer size from an otherwise inaccessible position to a point where gauging is possible.
A – The tapered roller bearing assembly with lower cone pressed into position on the shaft (B) and lower and upper cups in the housing but without upper coneC – Spacing element projects lower cone abutment face a known distance (x) (clear of shaft end)D – Gauging element projects upper cup track the same distance (x)E – Upper cone in gauging positionG – Gauging point (e.g. for low volume, a dial indicator, or for high volume, an electronic transformer – LVDT) arranged and pre-set to indicate spacer size (S)
In this schematic, a movable base (H) is shown which, by the application of a known force, seats the upper cone in its ‘projected’ track- the gauging element then giving a direct reading of the necessary spacer size. In practice, alternative methods may be used to suit any particular production facilities and requirements (for instance, a static base with the gauging load applied by a moving head from the top).
TYPICAL ACRO-SET APPLICATIONS
Examples where the ACRO-SET method has been successfully applied to tapered roller bearings include: manual transaxles, drop box transmissions, farm tractor axle assemblies, power take-off units, planetary pinions, differential and pinion shafts, gear reducers, and off-highway truck and tractor wheels.
PROJECTA-SET
The PROJECTA-SET technique is similar in concept and application to ACRO-SET, but adds additional versatility and sophistication through utilization of a special gauging fixture. This gauge enables one to “project” an inaccessible shim, spacer gap, or reference surface, to a position where it can be easily measured. This gauge typically incorporates the use of a dial indicator or an LVDT for measured readings. It is also readilyapplied in designs where the adjusting component (cone or cup) is tight fitted without sacrificing assembly speed or accuracy. The method (Figure 12) consists of two key gauging elements: a spacer sleeve (ref. C) and a tapered gauging sleeve (ref. D), of known (typically equal) design lengths (ref. X). These sleeves will project the inaccessible spacer gap beyond the shaft end. To illustrate the PROJECTA-SET method, reference a typical spiral bevel pinion shaft assembly (Figure 13). In this indirect-mounted cone adjusted design, the bearing setting is achieved through the use of a spacer located between the two cone front faces. The cups and cones are tight fitted in this application. The required gauging steps are:
- Place the assembled pinion shaft, except for the upper cone and spacer, on the press table. Position the gauge onto the upper bearing cup and apply the upper bearing cone (Figure 13).
- Activate the press to clamp the gauge through the two bearing cones. A known axial load is applied through the bearing cups at this time by the Belleville spring internal to the gauge. (Note that the press is required simply to clamp the upper cone in place, against the spacer sleeve, for proper seating. Some gauge designs accomplish this with a threaded nut design.)
- Oscillate the gauge (handles) to seat the bearing rollers. The LVDT probes then measure the axial displacement between the two gauging members and the required spacer size is displayed on the digital readout.
- The spacer size is determined by the gauge based on theformula (Figure 13): S = Z – A + K
- WhereS = Spacer size required.Z = Sleeve length (fixed).A = Variable distance between corresponding diameters on the tapers of cone and cup locator. (“Zeroed” dimension is known.)K = Constant to compensate for system deflection due to gauge spring load, mean tight cone fit effect (loss of clearance) and the desired bearing setting.G = Measured gap, which represents the change in distance “A”. Distance “A” includes “G”.
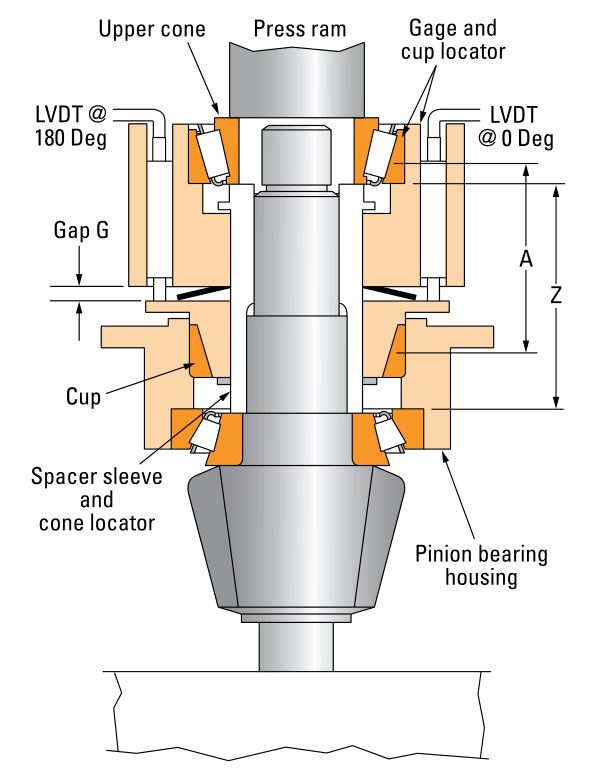
SPECIAL PROJECTA-SET CONSIDERATIONS:
- The size, weight, cost and design of the PROJECTA-SET gauge should be reviewed for specific application viability. Typical gauging cost for an industrial application, incorporating LVDT and internal gauge springs, is approximately $10,000 each. To increase set-up efficiency, higher volumes over 30,000 assemblies/year, the designer should consider design/usage of a special automated press and press fixture to apply the gauge.
- Separate gauges or interchangeable components (i.e. dual tapers) would be required if various models or shafts of the same application use a different bearing series.
- An alternate method of field servicing would be required to set the tapered roller bearings. (ACRO-SET is similar and should be given primary consideration.)
ADVANTAGES OF PROJECTA-SET:
- Prevents time consuming teardowns to change shims or spacers in an application with tight cone or cup fits.
- It can be readily applied to automated assembly processes.
- Human judgment is minimized when compared to past traditional manual methods.
- The use of PROJECTA-SET gauges requires minimum training time.
- The PROJECTA-SET method provides consistent and reliable settings.
TORQUE-SET
The TORQUE-SET method is based on the principle that the rolling torque in a preloaded bearing directly increases as a function of the applied preload force (typically measured by dimensional preload). Laboratory tests have shown that the torque variation of a new bearing is small enough to effectively use bearing rolling torque as a basis for predicting/gauging a consistent dimensional preload setting. This relationship (Figure 14) is established during pre-testing of several units and loads. Shims are added or subtracted after initial bearing rolling torque is measured to satisfy the desired bearing setting, either end play or preload. A shim chart is normally used to assist selecting the final shim pack for each unit (Figure 15).
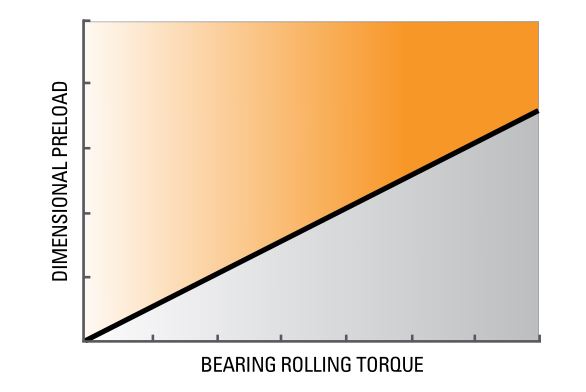
The steps required to perform the TORQUE-SET technique areoutlined below:
- Assemble the unit with a reference (constant thickness) shim pack that assures a preload in the system (Figure 16). Note the resulting bearing preload will actually differ for each assembly depending on the variations in the accumulated tolerances of the component parts.
- Measure the bearing rolling torque (Figure 17).
- Select the final shim pack thickness based on the preconstructed shim chart (Figure 15).
- Install final shim pack and complete the assembly by installing all cap screws (Figure 18).
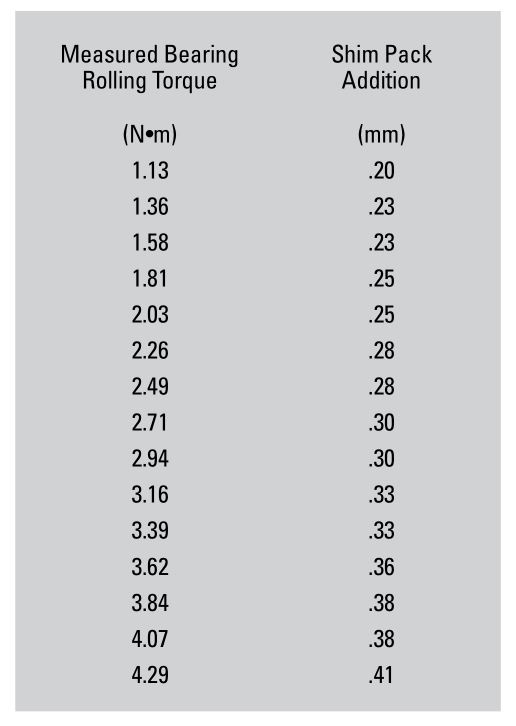
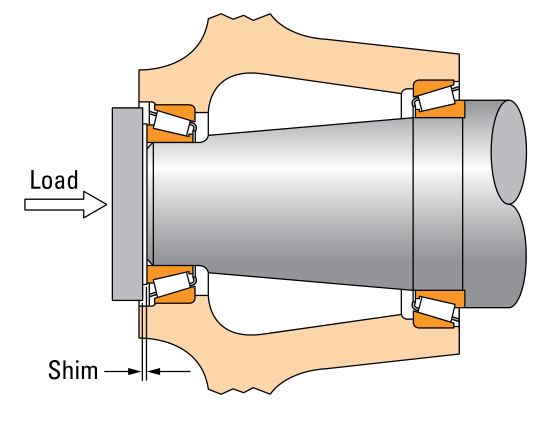
Bearing rolling torque is influenced by rotational speed and the lubricant being used. In any application using the TORQUE-SET approach, the lubricant and speed should remain constant.
The most common method of measuring bearing rolling torque is with a torque wrench.
Sometimes a socket can be used which fits over a nut on the end of the shaft or, if this is not possible, a special adapter can be made that fits the end of the shaft. In cases where the housing can be rotated, the torque wrench is adapted to the housing to measure rolling torque.
If a torque wrench cannot be used, a spring scale may be used to measure bearing rolling torque. Using a string wound around a gear or wheel and a scale, record the pull force needed to keep the assembly turning. Rolling torque is calculated by multiplying the radius of the gear or wheel around which the string has been wound by the pull force. This step could be avoided by a shim chart, which indicates pull force versus shimpack size.
When measuring bearing rolling torque, turn the shaft as slowly as possible while maintaining smooth rotation.
SPECIAL TORQUE-SET CONSIDERATIONS:
- Ability to Measure Rolling TorqueThe design must lend itself to measuring the rolling torque of the bearings. Where other components such as seals, piston rings, etc. contribute to the torque, provisions must be made to recognize and isolate these torque values from the bearing rolling torque. An example would be to record the drag torque of a shaft and seal in an end play condition then “add- on” the required bearing rolling torque for the preload condition.
- Ability to “Reseat” Tight-Fitted MembersWhen tight-fitted members are used for bearing adjustment, provisions must be made to “reseat” or back press that member after the TORQUE- SET load has been applied and the final shim pack determined.
- Bearing rolling torque is influenced by rotational speed and applied lubrication. These should be kept constant between units. The most common method of measuring rolling torque is with a torque wrench. When measuring rolling torque, turn the shaft as slowly as possible (estimated at 3.5 rpm) while maintaining smooth rotation.
- TORQUE-SET should not be used if there is an unbalanced load (created, for example, by heavy parts, clutch plates or caliper brakes). This would cause the torque to vary during rotation.
- For field servicing, the TORQUE-SET method should not be used to reapply previously operated (e.g. run-in) bearings. A new set of bearings or alternate technique must be used.
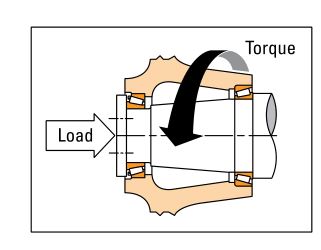
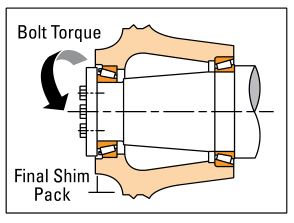
TYPICAL TORQUE-SET APPLICATIONS
TORQUE-SET has been used successfully on various industrial and automotive applications. Typical applications include pinion and differential shafts, transmission shafts, and gear box shafts.
ADVANTAGES OF TORQUE-SET:
- Usually, no special fixtures or tooling are required. A torque wrench or simple spring scale and cord is all that is needed.
- No shim gap measurements are required. The shim pack is simply changed to obtain the correct setting.
- This method is useful in equipment where manual methods are physically impractical or difficult. However, it may not be practical in very large equipment.
- TORQUE-SET can be applied to field servicing when new bearings are installed.
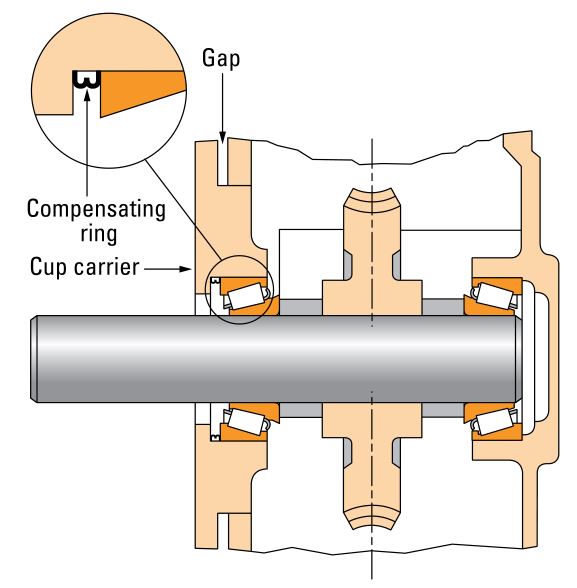
MOUNTING DESIGNS AND SETTING DEVICES
Tapered roller bearings can be mounted in various configurations and there are a variety of devices available to set the bearings to the desired end play or preload in an application.
CONE SETTING DEVICES
In an indirect mounting, generally one cone is backed against a fixed shoulder while the other cone is movable and backed bysome setting device.
A slotted nut (Figure 20) can be used for obtaining the bearing setting. The nut is locked in place with a cotter pin. Both the nut and washer should be of sufficient size to give adequate backing to the cone. Two cotter pin holes in the shaft, spaced 90 degrees apart, are used to obtain twice as many locking positions per revolution of the nut, and a corresponding closer bearing setting. A locknut, tongued washer and lockwasher can be used instead of a slotted nut (Figure 21). See the Auxiliary Parts in the Tapered Roller Bearing Guide for other locknut arrangements.
A stake nut (Figure 22) can be used for setting the bearings and by peening the thin section into a key- way slot locks it in place.
The setting in Figure 23 is obtained with shims and an end plate held in place by cap screws in the end of the shaft. A slot may be provided in the end plate to measure the shim gap. A type TDO bearing with cone spacer, above the centerline (Figure 24) and a type TNA bearing, below centerline, are manufactured with a fixed internal setting built into the bearing.
The type TDO bearing is shown assembled on the shaft with a cone spacer and clamped against a shoulder by an end plate. The type TNA bearing is assembled on the shaft with the cones butted together and similarly clamped against the shoulder. No further set-up provision is required in either case.
CUP SETTING DEVICES
In a direct mounting, generally one cup is backed against a fixed shoulder with the movable cup positioned by some satisfactory setting device.A cup carrier, Figure 25 above centerline, and cup follower, below centerline, uses shims for setting and the carrier or follower is held in place by capscrews.
SUMMARY
The fact that tapered roller bearings can be set is an advantage over other types of bearings. Manual setting has been considered an acceptable approach by many manufacturers and will continue to be used. The trend, however, is toward automated bearing setting procedures because of cost and more exacting performance requirements.
The selection of an automated bearing setting technique is best made early in the design stage. But, if the equipment is already designed and built, one or possibly a combination of setting techniques could be incorporated to improve setting reliability and reduce assembly time.
Contact your Timken sales engineer or service representative for further assistance in the proper selection of an automated bearing setting technique. The Timken Company team can assist with conceptual fixturing design, prototype testing, and implementation of techniques in production.
The Timken team applies their know-how to improve the reliability and performance of machinery in diverse markets worldwide. The company designs, makes and markets high-performance mechanical components, including bearings, belts, chain, gears and related mechanical power transmission products and services.
Setting Techniques for Tapered Roller Bearings – Setting Techniques for Tapered Roller Bearings –