M6410A, M7410F Actuators; V5862A, V5863A Valves67.5 LB (300N) NON-SPRING RETURN ACTUATORSAND 1, 1-1/4, 1-1/2 INCH NPT CARTRIDGE GLOBE VALVES
APPLICATION
M6410A and M7410F Series 3000 Non-Spring Return Valve Actuators provide floating or modulating control of V5862A and V5863A Series 3000 Cartridge Globe Valves.The actuators are used in electronic temperature control systems, which use hot and/or cold water (with glycol up to 50 percent) as the controlled medium in variable air volume (VAV) terminal units, fan-coil units, small reheaters, and coolers.
FEATURES
- Small size allows installation in limited space.
- Long-stroke allows a wider range of control.
Actuators
- Low power consumption.
- Synchronous motor.
- No mounting tools are required.
- Low-maintenance plastic housing.
- Conduit connector standard.
- No separate linkage is required.
- M6410A provides 3-position floating control without proportional feedback.
- M7410F receives 0 to 10 Vdc or 2 to 10 Vdc input signal, selectable at the site.
- M7410F includes a direct/reverse acting switch.
- Especially suitable for Excel® Controller or Individual Room Controller (IRC) System.
- Internal valve position indicator.
- Magnetic coupling for torque limitation independent of the voltage supply, and self-adjustment of the close-off port.
- Ready-to-wire connecting cable.
Valves
- V5862A is a two-way female NPT valve.
- V5863A is a three-way female NPT mixing valve.
- Pressure-balanced plug.
- A soft valve seat provides a low leakage rate.
- Valve inserts are changeable with the insert replacement tool.
- The threaded plastic cover allows manual operation.
- Brass body and stainless steel stem.
SPECIFICATIONS
IMPORTANTThe specifications given in this publication do not include normal manufacturing tolerances. Therefore, an individual unit may not exactly match the listed specifications. Also, this product is tested and calibrated under closely controlled conditions and some minor differences in performance can be expected if those conditions are changed.Models: M6410A: Non-Spring Return Valve Actuator. Provides floatingcontrol of the V5862A and V5863A Valves. M7410F: Non-Spring Return Valve Actuator. Providesmodulating control of V5862A and V5863A Valves. V5862A: Two-way NPT Valves. V5863A: Three-way NPT Mixing Valves.CAUTIONEquipment Damage Hazard. Installing a high-force (67.5 lb [300 N]) actuator on a 1/2 or 3/4 in. valve can damage the valve beyond repair. Use only Series 1000 (40.5 lb [180 N]) actuators with the smaller (1/2 in. and 3/4 in.) valves.IMPORTANT
- A low-force (40.5 lb [180 N]) actuator installed on a valve larger than 3/4 in. cannot operate the valve.
- Install high-force actuators (67.5 lb) only on large valves (1 in., 1-1/4 in., 1-1/2 in.).
Dimensions: Valves:See Fig. 1.Actuators: See Fig. 2.Control Modes:M6410A: Floating.M7410F: Modulating.Ambient Ratings:Operating Temperature Range:32° to 122°F (0° to 50°C).Storage Temperature Range: -40° to 158°F (-40° to 70°C).Humidity Range: 5 to 95% RH (noncondensing).Electrical Ratings:Input Power: 24 Vac, +10/-30 percent, 50/60 Hz.Power Consumption:M6410A: 0.7 VA.M7410F: 1.4 VA.Input Signal (M7410F): Modulating (adjustable) 0 to 10V, 2 to 10V, 0.1 mA.Input Impedance (M7410F): 100K ohms.Mounting: Actuator screws onto the valve body.Connections: 4.9 ft (1.5m) cable.
Weight:M6410A: 5 oz (0.15 kg). M7410F: 5.6 oz (0.16 kg).Stroke: 1/4 in. (6.5 mm).
Running Time:At 50 Hz: 150 seconds.At 60 Hz: 125 seconds.Stem Force: 67.5 lb (300 N).Suitable Medium: Water with a maximum of 50% glycol.Controlled Water Temperature: 36° to 230°F (2° to 110°C).
Rangeability:Two-way Valve: 50:1. Three-wayValve: 50:1 for the controlled port (A to AB).Flow Characteristic: Linear.Valve Cv Rating: See Table 1.NOTE:To determine the capacity index (Cv) needed for your application, use the following formula: Cv = gallons per minute divided by the square root of the pressure drop across the valve when the valve is fully open.Body Material: Brass.Stem and Plug Assembly: Stem: Stainless steel. Plug: Brass.
ORDERING INFORMATION
When purchasing replacement and modernization products from your TRADELINE® wholesaler or distributor, refer to the TRADELINE® Catalog or price sheets for the complete ordering number.If you have additional questions, need further information, or would like to comment on our products or services, please write or phone:1. Your local Honeywell Automation and Control Products Sales Office (check white pages of your phone directory).2. Honeywell Customer Care,1885 Douglas Drive North, Minneapolis, Minnesota 55422-4386International Sales and Service Offices in all principal cities of the world. Manufacturing in Australia, Canada, Finland, France, Germany, Japan, Mexico, Netherlands, Spain, Taiwan, United Kingdom, U.S.A.Actuator Required: M6410A: Non-Spring Return Valve Actuator (3-position floating).M7410F: 0 to 10 Vdc or 2 to 10 Vdc Electronic Actuator.Valve inserts are provided as spare parts. See Table 2.Leakage Rate: 0.05% of Cv.Valve Close-off Ratings: See Table 1.Approvals (Actuators): Underwriters Laboratories Inc. is listed for plenum use (UL94-5V).Accessories and Replacement Parts: WV3000R Insert Replacement Tool, for replacing cartridge insert.
Table 1. Valve Close-off Ratings. |
|||
Pipe Size inin. (mm) | Cv | Close-off Rating (psi) | |
Two-way | Three-way | ||
1 (25) | 5.5 | 232 | 232 |
7.8 | |||
11 | |||
1-1/4 (32) | 18 | 174 | 174 |
1-1/2 (38) | 25 | 145 | 145 |
Table 2. Valve Insert Replacement Parts. |
|||
Diameter (in.) | For Valve | Cv | Part Number |
Two-Way | |||
1 | V5862A3003 | 5.5 | 0903827 |
V5862A3011 | 7.8 | ||
V5862A3029 | 11 | ||
1-1/4 | V5862A3037 | 18 | 0903828 |
1-1/2 | V5862A3045 | 25 | 0903829 |
Three-Way | |||
1 | V5863A3002 | 5.5 | 0903827 |
V5863A3010 | 7.8 | ||
V5863A3028 | 11 | ||
1-1/4 | V5863A3036 | 18 | 0903828 |
1-1/2 | V5863A3044 | 25 | 0903829 |
FLOW DIAGRAMFOR 1, 1-1/4, AND 1-1/2 INCH VALVES
Fig. 1. Dimensions of V5862A and V5863A in. (mm).
Fig. 2. Non-Spring Return Actuator (M6410, M7410) dimensions in. (mm).
INSTALLATION
When Installing this Product…
- Read these instructions carefully. Failure to follow them could damage the product or cause a hazardous condition.
- Check ratings given in instructions and on the product to ensure the product is suitable for your application.
- The installer must be a trained, experienced service technician.
- After installation is complete, check out product operation as provided in these instructions.
- Before installing the valve and actuator, use the protective cover/manual handle to ensure the valve stem operates freely. An impaired stem operation can indicate a bent stem (due to rough handling). This condition can require replacing the valve.
- When installing valves, make sure the flow direction is correct by checking the arrow on the valve body.
- Mount the valve only with the stem pointing upward.
- Leave the protective cover in place until ready to attach the actuator.
LocationSelect a location where the valve and actuator are accessible.MountingValveThe valve body should be completely installed in the pipeline before the actuator is installed.
- Verify pipe size and flow direction for the valve being used.
- Position the valve so that the actuator can be easily installed.
- Install the valve using the applicable tools and supplies. Follow standard practices.
ActuatorNo tools are required to install the actuators on valves because they are threaded onto the valve by hand.
CAUTIONCareless Installation Hazard. Forcibly tightening the mounting connection can damage the valve and actuator. Never tighten the connection with a wrench. To mount the actuator, refer to Fig. 3 through 5. Fig. 4 shows the M6410A, M7410F valve position indicator: 1. Remove the protective cover from the valve (Fig. 3). 2. Make sure the actuator is in the (factory-supplied) OPEN position. 3. Screw the actuator connector onto the body of the valve (Fig. 5).WiringConnect the M6410A Actuator to the controller using the wiring diagram for the controller. See Fig. 6 for typical hookup to T6984F. For hookup with an Excel 10® see Fig. 7.Use the M7410F with Excel® 5000/500/100/80 Controllers, T7984, and W7751 controllers. Power the M7410F from the same transformer as the controller when using Excel Systems, or T7984 Controllers, when the common lines from the controller and the actuator are connected together and the hot side of the 24 Vac power connection on the transformer is used. See Fig. 8. The electrical installation must comply with the wiring diagram shown in Fig. 9.Fig. 3. Removing the protective cover from the valve.
Fig. 5. Mounting actuator to valve (M6410A shown).
Fig. 6. M6410A is used with T6984F.
Fig. 7. M6410A Actuator used with W7751D,F Controller.
Fig. 8. M7410F used with T7984F.
Fig. 9. Electrical installation showing wire colors and definitions.
Switch Selection (M7410F)The two built-in selector switches must be set according to the valve type (two-way or three-way) and the controller output signal (0 to 10V or 2 to 10V). See Fig. 10.
Input Signal Override (M7410F)To override the controller output signal, connect the input signal wire with COM (0%) or 24V (100%), see Fig. 11, using an external relay.If the temperature falls below a certain point; for example, 32°F (0°C), a relay can switch the 24 Vac to the Y connection (0 to 10V, 2 to 10V). This opens or closes the valve.
Fig. 11. Input signal override for frost protection.
OPERATION
Apply power to the actuator to drive the synchronous motor to turn a screw spindle that opens or closes the valve. The actuator is attached to the valve by a hand-tightened coupling ring and a magnetic coupling that limit the gear assembly torque and the actuator driving force.The actuator pushes the center stem of the valve down, compressing the valve spring and opening the valve. When the actuator reverses, the valve spring expands, closing the valve and pushing the center stem up.The valves are supplied with a threaded plastic protective cover/manual handle to protect the stem and to allow for manual operation. Use the protective cover/manual handle to fill the system during initial installation.
Turning the protective cover/manual handle:— Clockwise: pushes the center stem of the valve down, compressing the valve spring and opening the valve.— Counterclockwise: allows the spring to expand, pushing the center stem up and closing the valve.
NOTES:–You can also use the protective cover/handle for heating/cooling with neither a controller nor actuator during the building construction phase.–Retain the protective cover. It can be needed for future manual operation.
CommissioningA microprocessor within the actuator maintains accurate control/positioning by recommissioning itself every 24 hours or whenever power is applied or interrupted. When power is applied, the actuator drives to 0 and then to its starting position according to the starting/input signal. The initial commissioning or 24-hour recommissioning takes between 2.5 and 5 minutes, depending on the position of the actuator.
Valve Flow
TWO-WAY VALVESIn the two-way valves, the direction of flow is always from the inlet port to the outlet port as indicated by the arrows on the valve body (see Fig. 12).
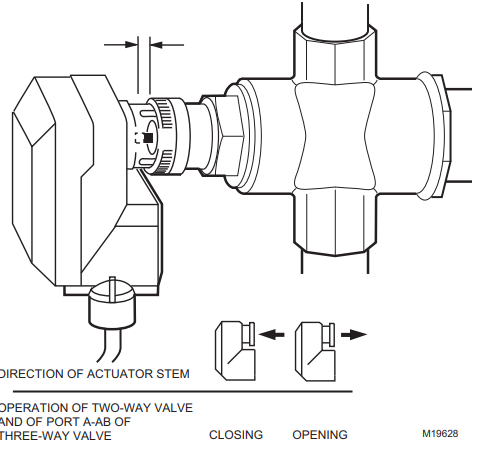
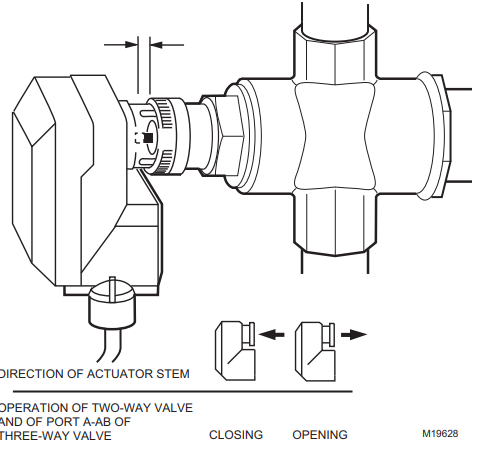
CHECKOUT
IMPORTANTOperating the system through one complete cycle is recommended to verify that the valve and actuator function properly.
ValveCheck Body and Connections for LeaksBefore installing the actuator, make sure that the valve stem operates freely by using the protective cover/manual handle. An impaired stem operation may indicate that the body was twisted by faulty piping or that the stem was bent by rough handling. Either of these conditions may require the replacement of the valve or cartridge insert.If leaking or other problems occur:
- Remove pressure from the valve.
- Remove the cartridge insert.NOTE: Instructions for removing and replacing the cartridge insert are packed with the WV3000R Insert Replacement Tool.
- Make sure the cartridge insert O-ring is properly seated and not damaged.
- After installing the actuator, check the actuator’s operation.
Actuator
Perform a functional checkout of the M6410A Actuator as follows:
- Change the room temperature setpoint by at least 10°F (6°C).
- Make sure the actuator either opens or closes the valve, depending on the direction of the temperature change. See Fig. 14.
- If the actuator stem moves in the wrong direction, reverse the connections for the blue and white actuator wires.
- If step 3 does not resolve the problem, replace the actuator.
Perform a functional checkout of the M7410F Actuator as follows:
- Change the Y input signal. The movement of the actuator stem (Fig. 14) indicates if the valve is opening or closing.
- If the direction of the valve stem travel is not correct, reset the direct/reverse switch.
By using this Honeywell literature, you agree that Honeywell will have no liability for any damages arising out of your use or modification to, the literature. You will defend and indemnify Honeywell, its affiliates and subsidiaries, from and against any liability, cost, or damages, including attorneys’ fees, arising out of, or resulting from, any modification to the literature by you.
Automation and Control SolutionsHoneywell International Inc.1985 Douglas Drive NorthGolden Valley, MN 55422customer.honeywell.com
® U.S. Registered Trademark© 2013 Honeywell International Inc.63-2612–05 M.S. Rev. 02-13Printed in the United States
[xyz-ips snippet=”download-snippet”]